Conventional plastics that are synthetically derived are not readily biodegradable and are considered as environmentally harmful. However, new biodegradable polymer blends have been developed to enhance the degradation of the final product. The use of biopolymers or bioplastics is based on renewable resources and contributes to material cycling, explain Arun Prasath Venugopal, Deepa Jaganathan and Aarthy Viswanath.
Table of Contents
In recent years, there has been a marked increase in the interest in the use of biodegradable materials in packaging. The principal function of packaging is the protection and preservation of food from external contamination. This function involves retardation of deterioration, the extension of shelf life, and maintenance of quality and safety of packaged food.
The most well-known packaging materials that meet these criteria are polyethylene or copolymer based materials, which have been in use by the food industry for over 50 years. These materials are not only safe, inexpensive, versatile but also flexible. For further insights into sustainable packaging methods, read about innovative ideas for single-use plastic substitution and biodegradable packaging potential and prospects.
Plastics are widely used in many applications such as in packaging, building materials, and commodities as well as in hygiene products. However, the problem of environmental pollution caused by the indiscriminate dumping of plastic waste has assumed a global proportion. However, one of the limitations of plastic food packaging materials is that it is meant to be discarded, with very little being recycled. These conventional plastics that are synthetically derived from petroleum are not readily biodegradable and are considered as environmentally harmful waste.
Most polymers are extremely durable and present a serious environmental problem, especially in urban centers. You can explore more about how sustainable food packaging is shaping the future to address these issues.
One option for the management of plastic waste is the use of biodegradable products. New biodegradable polymer blends have been developed to enhance the degradation of the final product. The use of biopolymers or bioplastics is based on renewable resources and contributes to material cycling that is analogous to the natural biogeochemical cycles in nature. Biodegradable polymers are the ones that fulfill all these functions without causing any threat to the environment.
The belief is that biodegradable polymer materials will reduce the need for synthetic polymer production (thus reducing pollution) at a low cost, thereby producing a positive effect both environmentally and economically. Learn more about the shift in the packaging industry through eco-friendly food packaging solutions.
Green Plastics Or Bioplastics
Green plastics or bioplastics are biodegradable plastics usually made from plants – a renewable resource. These plastics are biopolymers of long-chain compounds made up of long-chain molecule subunits. A biopolymer is an organic polymer which has been around for billions of years longer than synthetic polymers like plastics. The known biopolymers include starch, proteins and peptides, DNA, and RNA. These are biodegradable, eco-friendly and are obtained from natural sources. To understand more about innovative approaches in this area, you can explore the journey of green plastics and sustainable materials.
Biopolymers are polymers that are generated from renewable natural sources, are often biodegradable, and not toxic to produce. They can be produced by biological systems (i.e. micro-organisms, plants, and animals), or chemically synthesized from biological starting materials (e.g. sugars, starch, natural fats or oils, etc.). Biopolymers are an alternative to petroleum-based polymers (traditional plastics). For further insights, read about new technologies for sustainable packaging materials.
Green plastics focus on making convenient living consistent with environmental stability. The manufacture and disposal of green plastics involve environment-friendly processes. To produce green plastics, plant starch and soy protein are used as an alternative to petroleum-based products. Most cereal crops and tubers contain plenty of starch, which is converted into the plastic with the help of microorganisms. Green plastics were produced from corn, wheat, and soybean in the form of cellulose, starch, collagen, casein, soy protein, and polyesters. Discover more on the potential of agro-waste in producing green packaging.
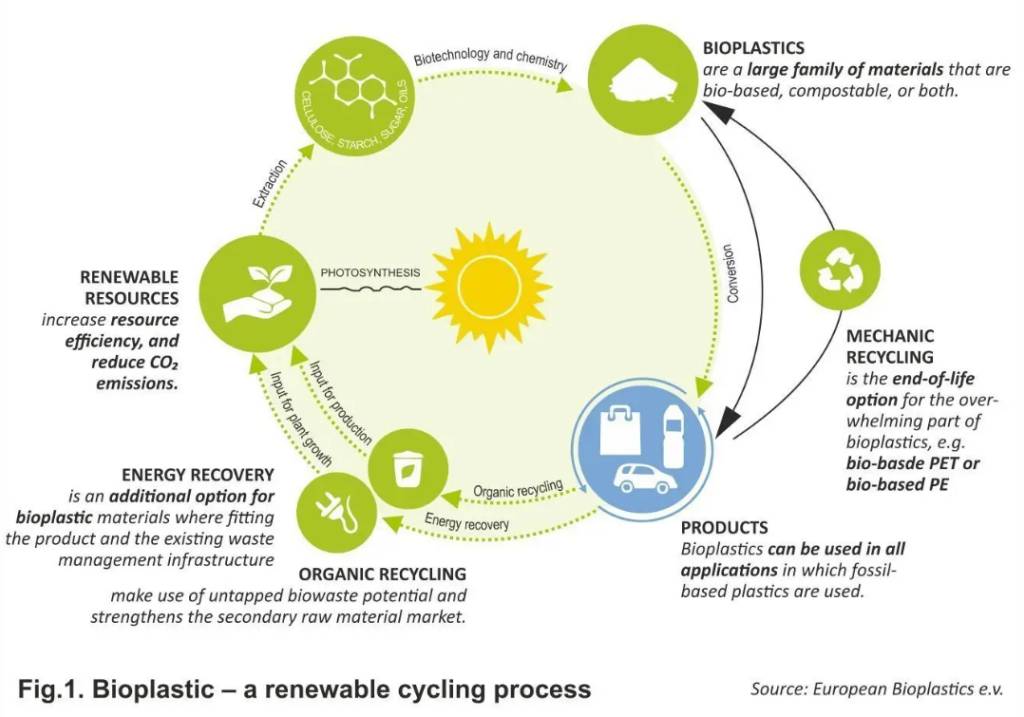
Definition of Green Plastics
Like all plastics, bioplastics are composed of a polymer combined with plasticizers, additives and processed using extrusion or thermosetting. What makes bioplastics “green” is one or more of the following properties. They are:
1. Biodegradable
2. Made from renewable ingredients
3. Environmentally friendly processing
Classification of Green Plastics
Biobased polymers may be divided into three categories based on their origin and production. They are:
1. Polymers extracted/isolated directly from biomass
2. Polymers produced by classical chemical synthesis and bio-monomers
3. Polymers obtained directly from natural or genetically modified organisms
1. Polymers extracted/isolated directly from biomass
Polymers of this category are obtained from plants, marine, and domestic animals. Examples are polysaccharides, such as cellulose, chitin and starch, whey protein, casein, collagen, soy protein, myofibrillar proteins of animal muscle, etc., can be used alone or as a mixture with synthetic polyesters such as polylactic acid (PLA).
Cellulose and derivatives: The most prevalent category that is used in food packaging is cellulose-based paper. There appears also regenerated cellulose film (cellophane paper) and cellulose acetate. Hemicellulose, the second most abundant plant polymer in the world, is in its infancy as biomaterial research for food packaging.
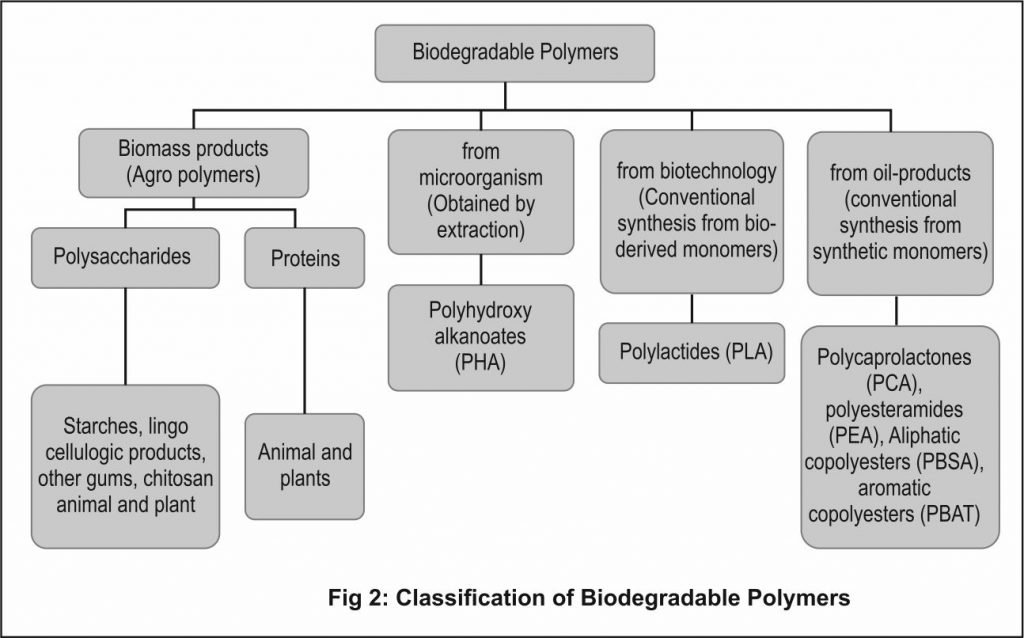
Starch: Green plants such as potatoes, corn, wheat, and rice are the raw materials for the production of biopolymers. Starch, as the main component in them, is potentially the most acceptable biodegradable polymer material due to its low cost, availability, and because it is produced from renewable sources. The nature of the crystal grains in the form of 15–100 microns in diameter after extraction, the crystal structure is distorted by pressing, heat, mechanical work, and plasticisers such as water, glycerol, and other polyols to make the thermoplastic starch (Bastioli, 2005). Plastic-coated starch (known as thermoplastic starch or TPS) is usually obtained by destroying or plastic coating native starch with water using the thermo-mechanical energy in a continuous extrusion process.
TPS can be manufactured in the same way as traditional plastics, but the sensitivity to water vapor and low mechanical properties render it useless for many applications. Mixing starch with aliphatic polyesters improves its workability and biodegradation. The combination of starch with a water-soluble polymer such as polyvinyl chloride (PVC) is used for the production of the starch film. This generation of plastics made from starch is completely biodegradable. From biodegradable plastics based on starch are made of different bags and sacks, rigid packaging such as hot-formed trays and containers, as well as products for filling gaps in packages. This material successfully replaces polystyrene and polyethylene in many applications.
Chitin and chitosan: Chitin is the second most abundant polysaccharide after cellulose and differs from it only by the OH group. The most abundant in the cell walls of the skin of insects, the shells of shellfish and insects, and can be found in the cell walls of some fungi. Chitosan is actually deacetylated derivative of chitin. Both are applied to produce various biodegradable films for packaging, and the largest they use as an edible coating to prolong the shelf-life of fresh fruits and vegetables. Chitosan has very poor mechanical properties and resistance to water.
More recently used composite films formed by mixing chitosan and starch show good properties when it comes to water vapour and mechanical properties. Chitin and chitosan have good antimicrobial properties against a variety of fungi, yeasts and bacteria found in food and thus enable good use as materials that produce biodegradable packaging for food packaging, in particular, are important for prolonging the shelf-life of foods.
Plant proteins: The two most common vegetable proteins used in the production of biodegradable packaging are chickpeas and isolated soy protein. Other proteins that are used include those extracted from wheat, pistachios, peas, and sunflower. Other polymers based on proteins such as albumin, casein, fibrinogen, silk, and elastin are taken into account due to its biodegradability as a raw material for the production of biodegradable packaging. Unfortunately, they have not found wide use because they are difficult to process, do not melt without decompression, and difficult to mix with other polymers due to incompatibility and processing them is expensive, unlike other polysaccharides.
2. Polymers produced by conventional chemical synthesis of bio-monomers
It is possible to get a large range of biopolyesters through chemical synthesis. The most famous of these groups of biopolymers is poly lactic acid (PLA-polylactide). PLA is biodegradable thermoplastic linear polyester, for its properties similar to polystyrene. The raw material for obtaining the lactic acid is obtained by fermentation of glucose or starch from any other source. As a source of carbohydrate may be used corn, wheat or alternatively whey and molasses. There are two principal monomers lactic acid and lactide.
PLA is mainly processed into thermoformed pads and containers for packing and serving food, films, transparencies, and bottles and other packaging blown but also mixed with other materials to improve their barrier properties. PLA has excellent water vapour permeability, which is important in the packaging of fresh food, which is necessary for the water vapor which evaporates quickly while reducing disturbance of the packaging.
3. Polymers obtained directly from natural or genetically modified organisms
Many bacteria accumulate these polymers as a source of energy and as a carbon reserve. This group includes polyhydroxyalkanoates (PHAs) and bacterial cellulose. PHAs are polyesters that are part of the living organism structure, hydrophobic and insoluble in water. Their characteristics are most associated with the properties of the monomer building blocks of which a wide variety of different biopolymer can be synthesized by microbial fermentation.
Depending on the bacteria and the carbon source, the polyhydroxy-alkanoate may be manufactured from rigid brittle to plastic to a rubber-like polymer. Have similar properties such as propylene and polyethylene, elastic and the thermoplastic (retained upon cooling forms). The most common is the use of derivative polyhydroxybutyrate (PHB). PHB is biodegradable polyester linear prepared by bacterial fermentation of sugar or lipid. It can be used for food packaging, cosmetics, and pharmaceutical products, as well as in agriculture.
Apart from renewable, biodegradable plastics can be produced from synthetic polymers by using bacteria. The bacterium Pseudomonas putida converts styrene monomer in the polyhydroxyalkanoate (PHA), biodegradable plastic which has a wide range of applications.
Properties of Biodegradable Materials
Materials were based on the need to be useful in the food packaging industry so as to their physical and mechanical properties enable their eligibility and the application of a certain degree, but it also applies largely to prices.
Barrier properties
Poor barrier properties (especially humidity resistance) of the traditional and most widely used biomaterials (paper, cellulose films, and cellophane) are all known and is, therefore, necessary to mix these materials with synthetic polymers to achieve the desired barrier properties for packaging of many foodstuffs. Biomaterials made of polysaccharides having poor barrier properties when it comes to water vapor and other polar substances in a large proportion of the humidity, but at the low or middle portion of humidity create good properties to oxygen and other non-polar substances such as various flavors and oils.
Moisture vapor transmission rate was prepared from the starch material is 4–6 times higher than conventional materials made from synthetic polymers. Materials made of arabinoxylan (barley) has low permeability as regards oxygen and CO2 and high permeability in the case of water vapor. Some of the barrier properties where the bio material and oil derived materials eg., PLA (polylactic acid) has a moisture vapor transmission rate 3–5 times greater than that of PET (polyethylenetere-phthalate), LDPE (low-density polyethylene), HDPE (high-density polyethylene) and OPS (oriented polystyrene). PLA has improved barrier properties to oxygen from PS (polystyrene), but not as well as PET.
PHA (polyhydroxyalkonate) has similar moisture vapor transmission rate as well as materials made from petroleum. PHB (polyhydroxy-alkanoates) has better barrier properties to oxygen from the PET and PP (polypropylene), and adequate barrier properties when it comes to fat and fragrances for products with a short shelf life. Barrier properties of gases in most bio-materials depend on the ambient humidity.
Mechanical properties
The mechanical properties of most organic material similar to the materials derived from petroleum. For example properties of the PLA are defined by molecular weight of the polymer chain structure (linear with respect to the branched), the degree of crystallization, etc. Orientation PLA improves the mechanical strength and heat stability, different molecular weight and crystallization result of soft and elastic to hard and high strength materials. The amorphous and poorly crystallized PLA has a transparent, shiny surface; a highly crystalline PLA has an opaque surface with the melting temperature of 130–180 °C.
Advantages of Green Plastics
- Less production energy than conventional plastics
- Non-toxic
- Sustainable and Degradable
- Reduced greenhouse gas emission
- Safe for medicinal use
- Starch-based bioplastics degrade 10-15 times faster than conventional plastics
Conclusion
Green plastics with a wide range of properties that could allow them to be processed like conventional plastics need to be developed. One of the real problems that exist is in defining and identifying green plastics. A venture between governments, industry and the society (such as BPI) could play an extensive role in educating the society what greenness truly means. Standardizations and certifications of sustainability should be publicized extensively. A globally accepted system of standards for green plastics could help manufacturers and producers to focus their efforts towards attaining a common target.
Infrastructure for collection and composting of degradable plastics need to be improved. Governmental incentives such as tax cuts and rebates could also help to promote greenness. Diversification of feedstocks from food crops to alternate biomass materials could have a positive impact on the cost as well as concern for using agricultural land. There seems to be a lot of enthusiasm among the society, industry and the governments regarding greenness. If the trend continues and the motivation for innovation in this field persists, the results could be promising.
References
- Bastioli C (2005): Starch-based technology, Handbook of Biodegradable Polymers, Shawbury, UK, Rapa Technology Ltd., 257–286.
- Battacharya M, Reis L, Correlo V, Boesel L (2005): Material properties of biodegradable polymers, Biodegradable Polymers for Industrial 3 Application, Cambridge, UK, Woodhead Publishing Ptd., 336–356.
- Funke U, Bergthaller W, Lindhauer MG (1998): Polymer Degradation and Stability, Volume 59, Issues 1–3, pp 293–296.
- Kolybaba, M, Tabil LG, Panigrahil S, Crerar WJ, Powell T, Wang B (2003): Biodegradable Polymers: Past, Present, and Future, American Society of Agricultural Engineers annual Meeting, Fargo, North Dakata, USA.
- Rustogy R, Chandra R (1998): Biodegradable polymers. Prog. Polym. Sci., 1273–1335.
- Weber CJ, Haugaarad V, Festersen R, Bertelsen G (2002): Production and applications of biobased packaging materials for food industry, Food Additives Contam,19: 172–177.
- Woo SI, Kim BO, Jun HS, Ho Nam Chang HN (1995): Polymerization of aqueous lactic acid to prepare high molecular weight poly (lactic acid) by chain-extending with hexamethylene diisocyanate, Polymer Bulletin, Volume 35, Issue 4, pp 415–421.
‘Processed Food Industry’: The Voice of Food Processing Industry
Processed Food Industry (PFI) is a premier English-language monthly B2B publication (ISSN 09721649) headquartered in New Delhi, catering to the vibrant and ever-evolving food processing industry. While we don’t claim to be the largest or most widely read, our proud legacy of over 27 years—publishing continuously since 1997—has earned us the trust of industry professionals as a reliable source of insights and information.
If your goal is to tap into the booming Indian and South Asian markets to promote your equipment, technology, software, or consumables, PFI is your strategic partner. With our hybrid approach across print, web, and social media, we help you establish strong brand recognition rooted in market relevance. Backed by a team of top-tier technical writers, we’re ready to work closely with you and your customers to craft compelling content that drives results.
India and South Asia’s food industry is expanding rapidly, driven by efficiency and cutting-edge innovations. Don’t miss the opportunity to elevate your brand and engage with this dynamic market. Get our 2025 media kit to fine-tune your marketing strategy, increase your visibility, and convert potential customers into valuable conversations. Additionally, ask for a sample copy of our monthly magazine and experience the quality and relevance we deliver.
Let us help you define your role in the future of the food processing industry.

Have a news or topic to share with industry? Write to us [email protected]