Typically, major food companies had access to robots, but collaborative robots or cobots are affordable, easy to use and have smaller footprints, making them accessible to all large or smaller enterprises, explains Sougandh K.M, Country Manager of India, Universal Robots.
Globally, industries are moving towards the adoption of new cutting-edge technologies. Automation has revolutionised the way operations are performed in the various sectors of the economy, jobs that were formerly carried out manually are now handled by robots, freeing up human labour for more productive endeavours.
In recent years, robots have become an integral part of every industry – manufacturing, automotive, plastic and polymers or the FMCG industry. Like every industry, the food and beverage sector also utilises automation to automate tasks like picking and placing, sorting, palletising or depalletising, packaging and many more. According to Business Research Company, the global food and beverage industry is predicted to reach $9,225.37 billion in 2027 at a CAGR of 6.3%, which is one of the market’s main segments.
Automation has reaped several advantages for producers in the food and beverage sector. Robotic automation has been very beneficial for manufacturers in helping them satisfy the constant demand from customers and maintain their competitiveness in the market. The manufacturing unit’s output has increased, and costs have decreased, thanks to automation significantly.
Here comes the role of robotics in the manufacturing of food. Typically, major food companies are dependent on some form of robotics technology. They now use advanced robots or man-machine solutions like collaborative robots (cobots) to perform a wide range of repetitive tasks. Earlier, only large companies have access to robots, but cobots are affordable, easy to use and have smaller footprints, making them accessible to all large or smaller enterprises.
Robots are utilised in the food and beverage business for various tasks, from removing raw food from the field to delivering the final product to customers’ doorsteps. At the early stage of food production, robots are employed for various tasks, including cleaning, product sorting, and blending. In the second stage, robots are used for packing, defect removal, mixing and sorting.
Cobots are often known as the companion of workers as they are safe to work alongside humans and reduce the risk of injury to a minimum, unlike industrial robots, which require fencing to operate. They are versatile and are capable of working around the clock. Besides, they can handle tasks like heavy weightlifting, which can be dangerous for humans Cobots are excellent at reducing expensive downtime, ensuring good quality, and maximising the use of their human staff for higher-valued tasks.
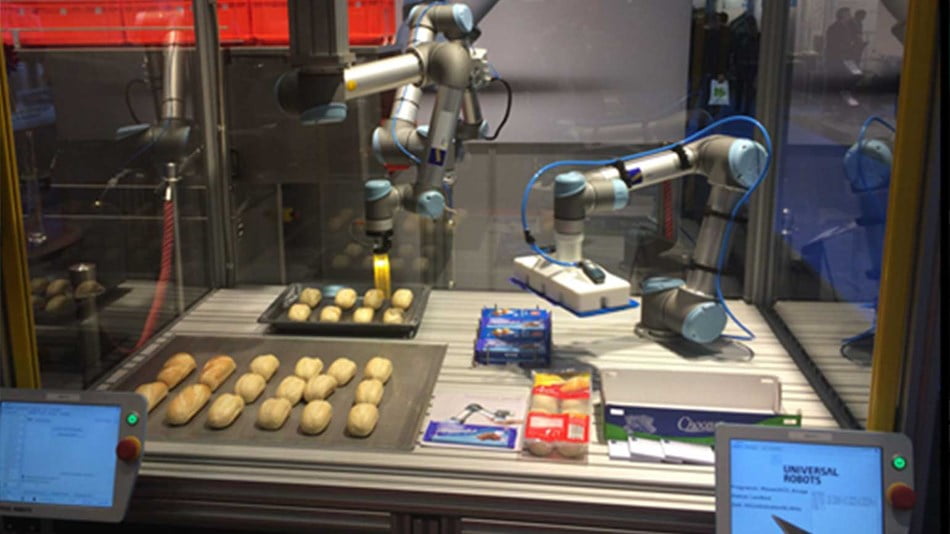
Benefits for food and beverage industry
Collaborative robots or cobots bring multiple benefits to the food and beverage industry, such as:
Keeping goods affordable
As the cost of energy and materials rises, maintaining the competitive price of pantry goods is a key concern. One of the key factors that could force the manufacturer to increase its prices is downtime, which cobots help it avoid. Cobots can work 24/7, decreasing the production process’s excessive labour cost and downtime, ultimately increasing the throughput.
Protecting workers’ safety
The safety of their employees is one of their top priorities and a significant obligation for manufacturers. Cobots can stop human workers from working in unpleasant settings or at odd hours. They take up arduous tasks, which free human workers from performing tasks that are dangerous to them.
For instance, In India, mass-food manufacturer Sri Lakshmi Agro Foods was established over 85 years ago and is responsible for some of India’s largest staple food brands, including Udhaiyam Dhall. The company sought to automate their production lines for greater consistency of output. It was especially concerned about finding the right solution for secondary packaging, which was solved with the deployment of the cobots. S. Sudhakar, Managing Director at Sri Lakshmi Agro Foods, found that UR’s human-friendly cobots were key in empowering the company to meet high levels of demand, especially during holidays like Diwali, by ensuring 24×7 output. Having a primarily female workforce, the UR5 cobot helper was particularly vital in enabling uninterrupted productivity so that women would not have to work late night shifts.
Utilising limited floor space
It’s not just task efficiency that cobots improve; manufacturing plants with minimal room on the floor can use them as a space-saving automated solution. Their built-in safety features allow them to operate safely alongside people without needing a cage or other bulky safety railings. Also, cobots have a smaller footprint and can be mounted to the ceiling as well. Another benefit manufacturers should be aware of is that the deployment of cobots requires minimal changes in the infrastructure, hence manufacturers need not worry about the additional cost incurred for installation.
Human error at critical stages
Human workers tend to get tired easily when performing repetitive tasks and tasks involved in harsh food production environments of intense heat, freezing cold or low-oxygen environments. Relying on humans at these critical points of food production may increase the risk of human errors, which can spell disasters for food through contamination by germs, pathogens and foreign objects. Even for simple, repetitive tasks, there is a potential for humans to make mistakes after a long period of time, which can negatively impact the quality of food products. These processes can be supported with reliable automated robotic systems to minimise the risk of contamination to almost zero.
FAQs on Automation in Food & Beverage Industry
How can Cobots bring flexibility to the food industry?
Cobots’ easy programming lets food and beverage producers and packagers quickly adapt to new products and delivery requirements. Collaborative robot arms can be reprogrammed, moved, and redeployed, so even smaller facilities can run multiple lines or switch from production to packaging in the same floor space.
How can Cobots improve productivity of food and beverage industry?
Cobots in food and beverage applications can work around the clock to meet even high seasonal demands. Quality isn’t sacrificed for productivity, with accurate, repeatable automation that can reduce waste. A wide range of plug-and-play grippers mean cobots can easily handle delicate and irregularly shaped objects.
How can Cobots improve Safety & Hygiene in F&B production?
Collaborative robots can be implemented to slow down or stop when working side-by-side with human operators in food and beverage processes. While our cobots are not suitable for primary food handling, they are being used widely for handling, packaging and palletizing of packaged foods and beverages.