Process pumps serve as the essential equipment necessary to the process of food processing. Hygienic applications must always adhere to strict regulations. Operators must ensure that their process pumps are cleaned thoroughly and adequately. That’s where a thorough cleaning process becomes mandatory, explains Paul Cardon.
Table of Contents
Some of the most stringent compliance regulations can be found in hygienic applications, a logical expectation considering that the equipment used in these industries must be sanitary. After all, processing food, cosmetics, and pharmaceuticals with dirty equipment or process pumps that have not been adequately cleaned can have devastating consequences for end-users.
That’s why hygienic applications require these regulations, which are established by varying regulatory agencies across the world, such as the U.S. Food and Drug Administration (FDA); the European Hygienic Engineering and Design Group (EHEDG); and the 3-A Sanitary Standards, Inc. These regulatory agencies provide a safeguard for manufacturers, as well as the public, to ensure that contaminated products don’t create additional safety hazards, such as food-borne illnesses and product recalls.
While the regulations serve as a means of safety for everyone across the supply chain, they can only go so far. A regulation, while useful, doesn’t solve the challenges that come from processing the substances that make up these industries. In general, the regulations establish a clean, sanitary environment, including proper cleanliness of the machinery involved. Process pumps serve as the essential equipment necessary to process and distribute these products to the world quickly and efficiently.
To achieve this, however, these pumps must process a variety of different products that can’t be susceptible to contaminants. That’s where a thorough cleaning process becomes mandatory. And while several process pump technologies are effective in hygienic applications, eccentric disc has multiple advantages that make it stand out against comparable offerings.
A lengthy cleaning process
Because hygienic applications must always adhere to strict regulations, operators must ensure that their process pumps are cleaned properly and thoroughly to comply with cleaning and sanitation procedures. Meeting those requirements, though, doesn’t come easy.
Disassembly is one option for keeping a process pump clean to meet regulatory standards. While this is a thorough cleaning option, it is not efficient and time-consuming. Many operators opt for the clean-in-place (CIP), which is far more efficient, yet not without its challenges.
A process pump in a hygienic application goes through a lengthy cleaning procedure that includes at least four separate rinses. A typical clean-in-place (CIP) procedure for a process pump in this situation includes removing debris or product recovery, followed by a pre-rinse and detergent recirculation. The next phase consists of an intermediate rinse and a second detergent recirculation, followed by an intermediate rinse and a disinfection phase. Once all those phases conclude, a final rinse occurs.
A typical CIP procedure for a process pump in this situation includes removing debris or product recovery, followed by a pre-rinse and detergent recirculation. The next phase consists of an intermediate rinse and a second detergent recirculation, followed by an intermediate rinse and a disinfection phase. Once all those phases conclude, a final rinse occurs.
Clean-in-place: Essential, yet problematic
These steps are thorough and necessary to meet regulations, yet they create several problems with many process pumps. Product recovery is the first thing to address before starting the CIP process. If a pump can provide compression and vacuum effects or run dry, then those capabilities are used to extract the product.
But often, the pump doesn’t have those capabilities, making it impossible to recover the product this way. One alternative method for product extraction comes from using a pigging system. With a pigging system, operators can recover residual product from pipelines using a projectile (also known as a pig) that cleans the pipes while moving the product to a recovery tank. This method cleans the pipes, saves the product within the pipes, and allows the CIP process to occur more effectively and efficiently.
Despite the benefits of a pigging system, it is not a foolproof solution. The major drawback to this method is the system does not effectively remove the product from pumps, valves, and filters. Some operators will turn to water and air flushing to address those areas, but this technique creates waste and product contamination.
When it comes to the CIP process itself, other problems arise. Excessive CIP flow rates, determined by in-pipe velocity (usually a minimum value of 1.5 to 3 m/s), are one of them. To properly clean a pump, the CIP flow rate must be turbulent, and it almost always comes in higher than the process flow rate.
The turbulent flow rate requires a bypass to mitigate an excessive internal pressure drop during the CIP process, yet this does not guarantee the proper cleanliness of the pump because no one can split the CIP flow rate between the bypass and pump.
Another problem during the CIP process is the water hammer, created by the speed of the CIP fluid before it reaches the process in the pump. When the fluid hits the process, it creates a shock or water hammer, which can cause considerable damage to the pump’s shafts and mechanical seal. One remedy is to put the CIP system close to the process, yet most systems are typically further away.
Temperature variations also create problems during the CIP process because fluid temperatures tend to range from 70°F to 200°F (20°C to 90°C). Process pumps with thin clearances will suffer under these varying temperatures, especially the rotating parts during the hot phases. Larger clearances, meanwhile, are better suited for these fluctuations yet can affect pump performance during certain process phases. Pump blockage can also occur if there is not a waiting period between hot and cold CIP phases.
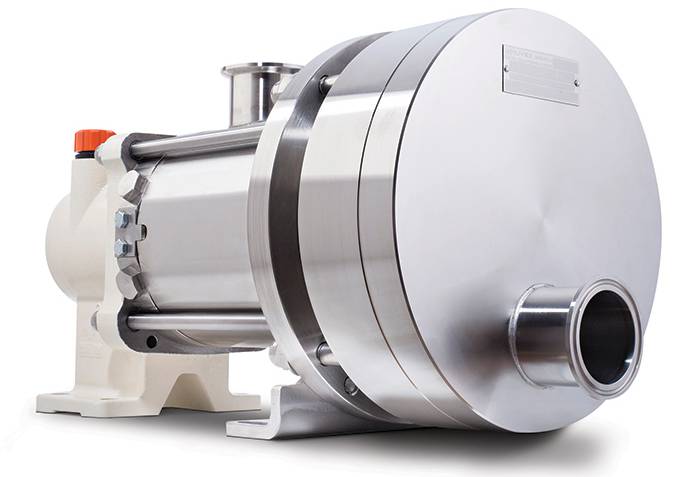
Why eccentric disc pumps are different
Eccentric disc pumps can overcome these CIP problems because of their design and versatility. These pumps consist of a cylinder and pumping element mounted on an eccentric shaft.
As the eccentric shaft rotates, the pumping element forms chambers within the cylinder, which increase in size at the intake port, drawing fluid into the pumping chamber. The fluid is transported to the discharge port where the pumping chamber size decreases. This action squeezes the fluid out into the discharge piping.
The pump’s design allows the CIP process to thoroughly clean it without adverse effects and can also incorporate the Easy Clean System. This Easy Clean System (ECS), which incorporates the bypass into the pump, allows reduced pressure drop inside the pump and even better cleaning. The ECS receives power from the solenoid valve used for the regular CIP bypass, as well as the compressed air source.
Mouvex offers two eccentric pump series equipped with an ECS – the SLS and H-FLO Series pumps. The design of these two models does not require an external bypass valve or linked piping. Instead, the transmission has a pressurized capacity that can handle 58 psi (4 bar) of compressed air, which opens the pump interior and allows the full CIP flow rate to pass through with limited pressure drop.
When processing a product, the eccentric disc pump’s transmission holds at atmospheric pressure, keeping the disc in contact with the cylinder to allow the pump to function properly.
The pump stops during the CIP process, and compressed air flows through the transmission. The compressed air stretches the bellows and pushes the disc away from the cylinder, allowing the CIP flow rate to pass through the pump with limited pressure drop. The compressed air also balances the internal and external pressure of the bellows, creating resistance to pressure and water hammers.
Product contamination is not an issue with eccentric disc pumps as they use the air that is already in contact with the product. Additionally, because eccentric disc pumps effectively remove the product before the CIP process starts, not as many detergents or fluids are required to clean it adequately.
Addressing the Common Clean-in-place (CIP) problems
By integrating the ECS into eccentric disc pumps, the common problems that plague other process pumps are mitigated. The eccentric disc pump design allows it to pump air, creating a vacuum effect on the pump’s suction side and a compressor effect on the discharge side. The design basically creates a plug effect, which forces the product out of the pump before the CIP process begins. Eccentric disc pumps also can recover product from transfer lines at rates as high as 95% on the suction side and 85%on the discharge side.
Product contamination is not an issue with eccentric disc pumps as they use the air that is already in contact with the product. Additionally, because eccentric disc pumps effectively remove the product before the CIP process starts, not as many detergents or fluids are required to clean it adequately. Eccentric disc pumps can have fewer soiled internals than other process pumps before the clean-in-place (CIP) process because of their ability to create a vacuum and compression environment within the pump.
With the ECS incorporated, eccentric disc pumps do not need a CIP bypass and can handle the full flow rate of the CIP process. Because these pumps can accept the full flow rate by staying fully open, the pressure drop decreases dramatically, and the cleaning process benefits, providing a more thorough and efficient cleanse. The lack of a CIP bypass also simplifies the installation, requiring less piping, which removes additional areas to recover product and clean.
Eccentric disc pumps also mitigate water hammer through the ECS system, which pressurizes the bellows. This action allows the pump to withstand higher CIP pressure (up to 90 psi [6 bar]) at the pump inlet, resisting the water hammer. Eccentric disc pumps also have a tangential suction port instead of a centered one, offering a cleaning advantage through the centrifuge effect and reducing the impact on the bellows.
The temperature variations from the clean-in-place (CIP) process also don’t impact eccentric disc pumps or the ECS because clearances are not needed within the equipment. In typical process pumps, functional clearances exist to prevent the internal parts from clogging or galling.
Eccentric disc pumps feature internal parts that remain in constant contact with each other, mitigating the need for clearances. The typical waiting period between hot and cold CIP phases also is not necessary, even with a 200°F (90°C) gap.
Conclusion
Process pumps serve as essential equipment in hygiene applications. Given the strict nature of regulations and standards, operators have multiple options to meet them by keeping their equipment clean and sanitary.
Of course, that cleaning process is not created equal for all process pumps. Using eccentric disc pumps paired with the ECS ensures that operators do not have to worry about the common problems associated with CIP and meeting regulations. An ECS-equipped eccentric disc pump gives manufacturers and operators a tool to overcome any CIP challenge, ensuring compliance with regulations. These pumps also help keep costs in line with fewer CIP steps and ensure high efficiency and functionality.
Author is Business Development Manager PSG Auxerre, France. He can be reached at [email protected].
*Mouvex is a product brand of PSG®, a Dover company, Oakbrook Terrace, IL, USA